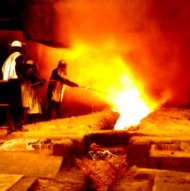 |
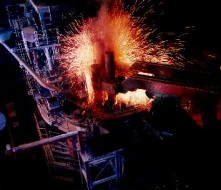 |
Die Versuche zur Gewinnung von Eisen auf elektrischem Wege
haben eigentlich schon vor mehr als 100 Jahren die Aufmerksamkeit
auf sich gelenkt Die allerersten Bestrebungen werden auf Werner Siemens zurückgeführt,auf dessen Anregung William
Siemens schon im Jahre 1870 mehrere elektrische Schmelzofen in
England entworfen und durch Patente geschützt haben soll. In
diesen ist auch der eigentliche Grundgedanke der mit Elektroden
arbeitenden Art von elektrischen Oefen die Erzeugung eines
möglichst grossen Licht bogens in der Schmelzgegend des Ofens
ausgesprochen. Es gab sehr viele Bemühungen, aber die Ergebnisse
waren grössten teils minderwertiges Eisen ausserdem erwiesen
sich die Anlagen meist als ausserordentlich kostspielig so dass
von einem rationellen Arbeiten nicht die Rede sein konnte, und so
blieb der weitere Ausbau dann über Jahrzehnte einfach liegen.
Aber, wie in der Geschichte schon des öfteren bewiesen der
Grundgedanke und sollte er auch in der hintersten Schublade vor
sich hindösen war gefasst und his er wiederentdeckt werden
sollte war an sich nur eine Frage der Zeit, oder vielleicht auch
nur des Zufalls. Erst ganz kurz vor der Jahrhundertwende haben
die vielen Bestrebungen Stahl in einem elektrischen Ofen zu
erzeugen zur endgültigen Ausbildung eines neuen Verfahrens
geführt: dem Elektrostahlverfahren. Emilio Stassano,ein
italienischer Artilleriehauptmann stellte 1898/99 vor also genau
100 Jahren erste Versuche in einem elektrischen
"Schachtofen" zu erschmelzen den er mit Hilfe der Soc.
Siderurgica Comuna in Darlo aufstellen konnte Hierbei soll es
gelungen sein aus allerdings sehr reinen Eisenerzen verschiedene
weiche Eisensorten betriebsm„ssig herzustellen Aus Mangel an
wirtschaftlichem Erfolg wurden die Versuche jedoch bald wieder
eingestellt. Aber es ergaben sich daraus sehr wertvolle
hüttenmännische Beobachtungen die der späteren
Weiterentwicklung von sehr grossem Nutzen sein sollten.
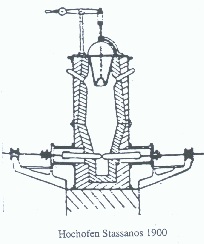
|
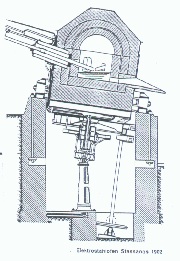
|
Aus den
bei Stassano Versuchen gewonnenen Erfahrungen war mit Recht zu
folgern dass es unwirtschaftlich war die Reduktion der Erze
(reduzieren=Entzug des Sauerstoffs in einem Oxid) und die
nachfolgende Reinigung sowie Entkohlung des Roheisens in
"ein und demselben" Schmelzraum vorzunehmen. Die beiden
genannten Vorgänge finden grundsätzlich in von einander
getrennten Oefen statt es wird also der "Hochofen"
wieder streng von dem "Stahlofen"geschieden. Eine
wichtige und wertvolle Erkenntnis. Aehnlich sah es auch beim
elektrischen "Hochofen" von Heroult aus der zunächst
von der "Soc.Electrometallurgique Française" in Froges
(Isére) zu Versuchen aufgestellt wurde. Das hier erzeugte
"Roheisen" wurde in einem nach Art
"Martinofen" arbeitende, ebenfalls elektrisch beheizten
kippbarem "Reiniger" in Stahl übergeführt. Zum
Entkohlen wurde dabei Schmiedeeisenschrott im kaltem oder warmem
Zustand verwendet.
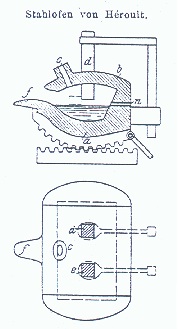
|
|
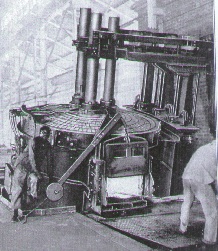
|
In einem bedeutsamen Schritt in Richtung Eisen
auf elektrischem Weg zu erzeugen war es P.Héroult gelungen
Werkzeugstahl herzustellen. In La Praz (Savoyen) hatte seine
(obengenannte) Gesellschaft seit ihrem ersten Versuch im Jahre
1900 bereits 2500 to. Stahl hergestellt. Bei dem Verfahren wurde
ein geschlossener Ofen mit zwei Kohleelektroden angewandt, die
unabhängig voneinander selbsttätig vorgeschoben werden und
während des Schmelzens nicht in das Bad eintauchen. Beim
Schmelzen kommt das Schmelzgut mit Luft oder mit Feuerungsgasen
nicht in Berührung. Nach Beendigung des Schmelzverfahrens wird
der Ofen gekippt,die Schlacke abgegossen und der Stahl in Formen
gegossen. Es wird diesem Stahl nachgerühmt dass er billiger sei
als Tiegelstahl und dass er frei von Gasen ist, keine Risse oder
innere Spannugen aufweise. Im Jahre 1905 schreibt VDI Bei der
Herstellung von spezialstählen deren analytische Zusammensetzung
genau eingehalten werden muss, wirkt die Anwesenheit von
Kohleelektroden störend, weil sie auf den Kohlenstoffgehalt des
Stahles von Einfluss sind. Auch die Verwendung von
wassergekühlten Stahlelektroden vermag dem nicht abzuhelfen.
Hier aber kann der von Kjellin bereits 1900 erfundene
elektrodenlose Schmelzofen ganz gute Dienste leisten, der auf
einem der grössten der bisher bestehenden elektrischen
Stahlwerke ,dem von Benedicks in Gysinge (Schweden) arbeitet.
Dieser Ofen stellt in seiner Art sozusagen einen Transformator
dar und hat den Vorteil dass man ihn mit verhältnimässig hoher
Spannung speisen kann. In Gysinge sind mehrere solcher Oefen von
80 bis 1800 kg Fassungsvermögen aufgestellt.
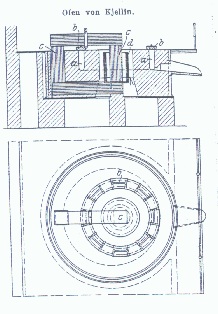
Später hat sich eine besondere Abart des Kjellinschen
"Induktionsofens" entwickelt, der wegen seiner
mannigfaltigen Vorteile in steigendem Masse Anwendung gefunden
hat, der "kernlose" Induktionsofen (früher auch
Hochfrequenzofen genannt) Seine Bauart ist sehr einfach es ist
ein tiegelförmiges Schmelzgefass, das sich in einer
wassergekühlten Kupferspule in die der Strom der von einem
Umformer kommt, geleitet wird. Die durch die Induktionsströme in
dem metallischen Einsatz gebildete Wärme erhitzt das Bad und
wird von diesem auch auf die darüber gebildete Schlacke
übertragen,so dass die erforderlichen Umsetzungen zwischen Stahl
und Schlacke stattfinden können.
(Aus:Technik des Eisenhüttenwesens VDE 1939)
Darüber hinaus gab es noch eine grosse Reihe der verschiedensten
Bauarten die entwickelt wurden und die auch mit mehr oder weniger
Erfolg Eingang in die Praxis gefunden haben. So seien besonders
als wohl wichtigste Vertreter die Oefen von Frick-Keller
Nathusius und insbesondere der Röchling-Rodenhauser Ofen
hervorgehoben. Sie Alle hatten eine Gemeinsamkeit nämlich den
elektrischen Strom als Warmequelle zu benutzen, nur, in der Art
und Weise wie die Umwandlung der elektrischen Energie in Wärme
erfolgte unterschieden sie sich. Dr.M. Ungeheuer schrieb 1910
hierzu: Als Typus der "Lichtbogenerhitzung" gilt das
Stassano-Verfahren während das ursprüngliche Heroult Verfahren
für die vereinte "Widerstands-Lichtbogenerhitzung"
bezeichnet wird, wohingegen das Kjellenverfahren von diesen
beiden insofern weit abweicht, als bei ihm durch Verwendung eines
Transformatorofens die zu erhitzende Substanz selbst den in den
Stromkreis eingeschalteten Leitungswiderstand bildet Es handelt
sich also in letzterem Fall um eine direkte Widerstandserhitzung
die in elektrodenlosen "Induktionsöfen" eine Erfindung
de Ferrantis vor sich geht. Allein die ersten Induktionsöfen
erwiesen sich im Betrieb als sehr kostspielig und erforderten
auch aussergewöhnlich teure elektrische Maschinen. Erst mit dem
Bau der Drehstromöfen System
"Röchling-Rodenhauser"der Elektrostahlanlagen GmbH
Berlin wurden diese Hindernisse bezwungen.
Anfangs war man auch
der Ansicht dass nur in kleinen Oefen von 2 bis 5 to. Stahl mit
grosser Gleichmässigkeit und kleinsten Schlackeneinflüssen zu
erzeugen sei. Dementsprechend waren auch die ersten Oefen
ausgelegt. Es sollte sich aber schon sehr bald herausstellen dass
dies ein Trugschluss war. Die Erfahrung lehrte nämlich dass es
auch möglich war in grösseren Oefen Stahlqualitäten
herzustellen die höchsten Ansprüchen gerecht wurden. In den
grossen Ofeneinheiten tritt als Folge der starken Ströme eine
lebhafte Durchmischung des Bades ein und durch gezieltes
metallurgisches Vorgehen kann die Bildung unangenehmer
Schlackeneinflüsse verhindert werden So kam man nach und nach zu
Ofeneinheiten mit grossem Fassungsvermögen. Von den beiden
Hauptofenarten Lichtbogen und Induktion setzte sich im Laufe der
Zeit der Lichtbogenofen durch. Betriebliche Vorteile insbesondere
eine schnelle Betriebsbereitschaft und die Unabhängigkeit von
der Beschaffenheit des Einsatzes gaben den Ausschlag. Weitere
grosse Vorteile waren zweifellos seine bessere Haltbarkeit und
die Möglichkeit einer schnellen Ausbesserung. Von den
Zahlreichen Bauarten an Lichtbogenöfen hat sich schlussendlich
der Heroult Lichtbogen-ofen durchgesetzt. 1905 wurde der erste
"Heroult Ofen (Patentiert 1900) in Deutschland bei den
Richard Lindenberg Stahlwerken in Remscheid unter Leitung von
Fr.H.Eichhoff in Betrieb genommen. Bauart Heroult-Lindenberg. Er
gilt allgemein als der Vorfahre unserer heutigen modernen Anlagen
,auch in Luxemburg.
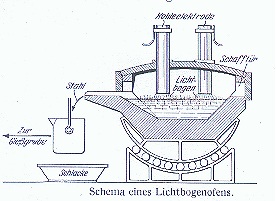
Elektrostahlwerk Dommeldingen.
1908 wollte
man in Dommeldingen,das damals 3 Hochöfen mit einer jährlichen
Kapazität von etwa 110.000 to. Roheisen besass einen neuen Weg
beschreiten. Es war aber nicht einer der sonst üblichen Wege die
Angliederung eines Thomasstahlwerkes sondern man versuchte sich
die Erfahrungen auf dem Gebiet der elektrischen Stahlherstellung
zunutze zu machen.
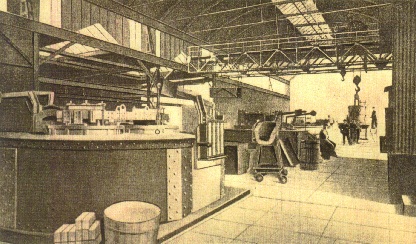
Die Idee kam von Emile Brian Werksdirektor von
1900 bis 1918 Die ersten Versuche im August 1909 erfolgten in
einem 700 Kg Induktionsofen Röchling-Rodenhausen. Sie
rechtfertigten 1911 den Bau von 3 Induktionsöfen mit je 3500 kg
Leistung und eine weiteren von 500 kg Leistung. Sie waren
ebenfalls Bauart Röchling-Rodenhausen. Es soll, so verlautete
damals die Verarbeitung der luxemburgischen Eisenerze vermittels
dem E-verfahren ein ungewöhnlich gutes Resultat gezeigt haben.
Erste Ergebnisse sprachen sogar von einem Stahl der sich mit dem
anerkannt guten schwedischen Stahl vergleichen liess. Das
flüssige Roheisen aus dem Hochofen wurde in einem kippbaren
Mischer Typ "Wellmann" (Gasgeheizt) vorbereitet 1913
wurde ein Martin-Ofen von 30 Tonnen in Betrieb genommen, der
anfangs von Hand beschickt wurde, später 1923 mit einer
mechanischen Lademaschine. Man sollte zwischendurch nicht
unerwähnt lassen dass die Dommeldinger Hochöfen aus Koksmangel
während des ersten Weltkrieges gedrosselt und 1920/21 sogar
stillgesetzt wurden. 1922 nahmen sie die Produktion teilweise
wieder auf, um aber 1927 definitiv ausser Betrieb zu gehen. Das
erste Elektrostahlwerk funktionierte bis 1929 Danach übernahm
ein Lichtbogenofen Typ Heroult mit 3 Elektroden und einem
Fassungsvermögen von 8 Tonnen, später 10 Tonnen die Nachfolge
der alten Induktionsöfen. 1936 wurde ein kleiner Ofen von 600 kg
gebaut und 1943 ein weiterer Ofen ähnlich dem ersten. 2
Induktionsöfen (kernlos) mit einer kapazität von 1500 kg
resp.500 kamen 1954 resp. 1957zu ihren ersten Einsätzen .Der
erste Héroult wurde 1962 ersetzt durch eine moderne kippbare
Ausführung der die Beschickung per Korb erlaubte. Dies war ein
grosser Fortschritt.Der Martin-Ofen und der Wellmann Mischer
stellten 1950 de Betrieb ein. (ARBED Un demi-siecle d'histoire
industrielle 1911-1964 )
Vom Hochofen zum Elektroofen. Die in einem Elektroofen
verlaufenden metallurgischen Vorgänge ähneln in ihren
Grundzügen denen in einem Siemens-Martin-Ofen vor sich gehenden
Reaktionen. Man verarbeitet hauptsächlich Schrott, dem man nach
Bedarf Roheisen zusetzt.Wenn man, wie nun in Luxemburg vollzogen
alle Hochöfen ausser Betrieb setzt und auf E-Stahl umsteigt,
stellt sich doch die Frage nach dem Bedarf an Schrott und dem
Schrottaufkommen. Woher der Schrott kommt, welche Qualität er
hat und die wohl wichtigere Frage wie lange man Schrott für den
E-Ofen auf dem Markt haben kann, womit sich auch gleich die
Preisfrage anschliesst, dürften auch manchen Laien
interessieren. Woher der Schrott kommt? Die Antwort auf diese
Frage muss man gleich schon unterteilen:
a) Bei der Herstellung des Stahls fällt bereits im Stahlwerk und
anschliessend im Walzwerk Schrott an, der auch weiterverarbeitet
werden kann. Das war früher in viel grösserem Ausmass der Fall,
heute ist dieser Anteil durch die neuen Stranggussanlagen weitaus
geringer geworden. Stahlwerk und Walzwerk werden in Zukunft nicht
mehr sehr viel Schrott hergeben.
b) In der "stahlverarbeitenden" Industrie fällt
ebenfalls Schrott an, aber auch hier gilt genau wie unter a) die
immer moderneren Anlagen sowie die viel bessere Auswertung der
Installationen bewirken dass Schrott auch hier Schrott zur
Mangelware wird. Am deutlichsten lässt sich das aus der Tatsache
ableiten dass diese Betriebe nur noch sehr wenige und kleine
Mengen an Material stockieren im Gegensatz zu früher wo riesige
Lagerplätze oft grösser als der Betrieb selbst, nötig waren.
Dabei ist auch dieser Schrott wie unter a) ein wertvolles
Produkt. Beide lassen sich relativ einfach wieder in den
Kreislauf des E-Verfahrens einbringen. Schrott hat als wertvolles
Produkt seinen Preis.
c) Es bleibt noch der sogenannte Altschrott der in unserer heute
so modernen Welt in grossen Mengen anfällt. Aber mit dem allein
kann man "nicht viel Staat" machen. Allein die
Aufbereitung verlangt schon grosse Investitionen und die
Qualität wird sicherlich nicht besonders gut sein wenigstens
nicht im Vergleich zu den beiden vorgenannten Aus dieser
Erkenntnis erhebt sich die Frage : Wird das Angebot an diesem
"minderwertigen " Schrott Bestand haben? Man kann nicht
unbedingt "guten Schrott mit minderwertigem verkochen und
daraus eine anständige Stahlsuppe erwarten.
d) Im Elektroofen werden aber in zunehmendem Masse sogenannte
"Schrott-Ersatzstoffe "eingesetzt in Form von
"Eisenschwamm" (HBI/DRI/Eisenkarbid) oder Roheisen
(fest oder flüssig) HBI= hot briquetted iron in Form von
Eierkohlen) DRI= direct reduced iron (Granulat) Beides ist
Eisenschwamm und wird durch Reduzierung von Eisenerz gewonnen.
Einerseits liefern diese "Ersatzstoffe" einen Zusatz an
reinem Eisen und verdünnen damit die Unsauberkeiten des Schrotts
(Wie Kupfer Chrom usw.) andereseits haben diese Stoffe festere
Weltmarktpreise und können demzufolge die stark schwankenden
Schrottpreise in "etwa" ausgleichen. Bemerkenswert ist
in diesem Zusammenhang vorallem die Tatsache dass sich ARBED in
Zusammenarbeit mit PAUL WURTH der Entwicklung eines Verfahrens
zur DRI-erzeugung verschrieben haben. Dieses Verfahren soll
sowohl auf Basis von Feinerzen als auch von Abfallstoffen
(Staub-Sinter usw.) der Roheisen und Stahlerzeugung
funktionieren. Es gibt also keine eindeutige Trennung mehr
zwischen Konverterstahl und E-Stahl da vorreduzierte Erze
(Eisenschwamm) im E-Ofen eingesetzt werden und so kann der
E-Stahl langsam seinen Einzug in den Flachprodukten (Bleche)
halten. Dabei wird das Wachstum beim E-Stahl stärker sein als
bei dem Konverterstahl, da die Investitionenskosten für die
tradionelle Stahlerzeugung über Hochöfen und
Konverterstahlwerke enorm hoch sind. Vor etwa 25 bis 30 Jahren
ist der Stahlverbrauch jährlich um 4 bis 5% gewachsen heute sind
es nur noch 2 bis 3% (allerneueste Feststellungen reden wieder
von 5%) In unseren Industrieländern ist zwar ein geringer aber
noch wachsender Stahlverbrauch festzustellen Hingegen dürfte in
sogenannten Entwicklungsländern und den ehemaligen
Ostblockländern ein höherer Zuwachs an Stahlverbrauch zu
erwarten sein. Weltweit wird es einen nicht ganz steilen aber
immerhin noch recht bemerkenswerten Anstieg geben. Die Hochöfen
werden sich näher an den Rohstoffquellen ansiedeln.
(Seehäfen-Erz und Kohlegruben ) Vorallem aber werden in vielen
Werken eine Anzahl von kleineren Hochöfen durch einzelne und
leistungsfähigere Hochöfen ersetzt. Die Verlagerung und die
Modernisierung der Roheisenproduktion wird sicherlich noch einige
Jahrzehnte dauern. Wie dem auch sei , der Anteil an
Konverterstahl und damit auch der Roheisenproduktion werden nicht
rückläufig sein. Sicher fehlen in diesen meinen Uberlegungen
viele wertvolle Argumente die ein Aussenstehender nicht kennen
kann, die aber dazu beigetragen haben dass dieser Weg
eingeschlagen wurde. Nach neuestem Stand sollen die beiden
letzten Hochöfen "A" und"B" als nationale
Monumente klassiert werden. Somit bliebe uns die vertraute
Silhouette auf die wir immer stolz waren, wenigstens teilweise
erhalten. Eine Erinnerung an vergangene Zeiten die uns dann
niemand wird nehmen können.
|